European Space Thermal Engineering Workshop 2023
Einstein and Newton
ESA/ESTEC
INTRODUCTION
The European Space Thermal Engineering Workshop, organised by the ESA Thermal Division, will be held on:
Tuesday 10 to Thursday 12 October 2023
at ESA/ESTEC, Noordwijk, the Netherlands.
The event is held live at ESTEC only, not hybrid or on-line!
Aim and scope
The aim of the workshop is:
- to provide a forum for the exchange of views, experiences, best practices and lessons learned from thermal engineers involved in space missions
- to promote and facilitate contact between thermal engineers and thermal technologies and tool developers
- to present recent developments on all aspects related to the thermal engineering domain and to solicit feedback
- to present new approaches and methodologies (e.g. for thermal design, analysis and verification)
Topics covered include in particular
- thermal design (for platforms, instruments etc.)
- thermal analysis and software tools
- thermal testing
- thermal control technologies
- two-phase heat transport technology
- thermal technologies and methodologies related to small satellites and CubeSats
- mapping of thermal results to mechanical models and guidelines for thermo-elastic (for thermal part)
- Lunar Night Survival
Organisation
The workshop will consist of presentations only. The working language will be English.
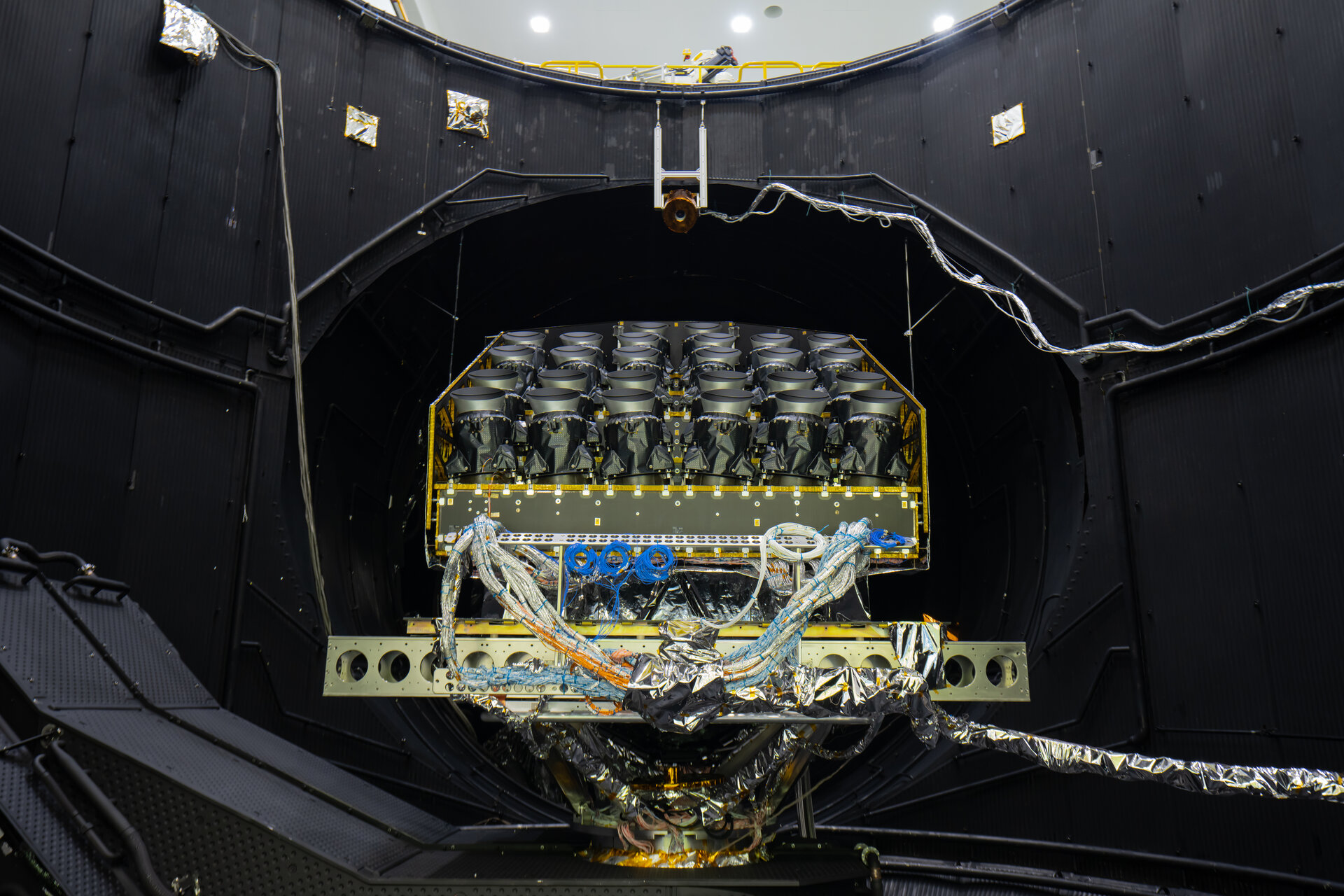
Plato-S Cave Vacuum Test for Exoplanet Detection
-
-
08:30
Registration Newton
Newton
-
Opening Newton
Newton
Convener: Dr Harrie Rooijackers (ATG-Europe)-
1
Opening
Opening of the workshop
Speaker: Dr Harrie Rooijackers (ATG-Europe)
-
1
-
ESA Missions and Thermal Technology Development Update: Contribution Stephane Lapensee Newton
Newton
Convener: Dr Harrie Rooijackers (ATG-Europe)-
2
ESA Missions and Thermal Technology Development Update Newton
Newton
Speaker: Stephane Lapensee (ESA)
-
2
-
11:00
Coffee Break Einstein and Newton
Einstein and Newton
ESA/ESTEC
Keplerlaan 1 2201 AZ Noordwijk The Netherlands -
Cube Sats Einstein
Einstein
Convener: Malgorzata Solyga-
3
Thermal control design for AcubeSAT's biological experiment and proposed model correlation method
Out of nearly two thousand CubeSat missions that have taken place, less than ten have been designed to cultivate and sustain living organisms in-orbit whilst working with as strict thermal requirements as the AcubeSAT, developed under ESA Education's “Fly Your Satellite! 3 Programme” by SpaceDot. SpaceDot is a non-profit, volunteer, and interdisciplinary student team working on the 3U CubeSat project AcubeSAT, supported by the Aristotle University of Thessaloniki (AUTh), Greece. The team comprises more than 60 students from AUTh and several other universities across Greece and Europe.
The mission's goal is to study the effects of microgravity and radiation on eukaryotic cells using a compact microfluidic platform (Lab-on-a-chip) located inside a sealed container (payload) that houses the biological experiment under atmospheric conditions. Currently, the development cycle of the Payload Container is nearing its end and environmental testing at the CSF facility is scheduled in the near future.
By its nature, the CubeSat platform poses challenges in the integration of traditional thermal control methods. Whether that is attributed to a strict mass/power budget or limited space to implement proper thermal insulation from the harsh environment of space, maintaining the satellite's biological payload at optimal temperatures to promote cell growth presents a great challenge. Therefore, meticulous thermal modeling and rigorous design optimization plays a crucial role in the development process.
The objective of the aforementioned tests is to validate the passive and active thermal control system and improve the thermal mathematical model. Some of the challenges the thermal subsystem is facing is working within the confines of a sealed vessel that houses a variety of temperature-sensitive components where the experiment will be held. Some of them are, the microfluidics chip where the experiment will be conducted, the solenoids that will transfer the growth medium to the eukaryotic cells and the bags that will contain said growth medium. Because the container is filled with air, the analysis must account for the fact that the tests will be conducted on earth where, unlike in orbit, the DUT is subject to gravity and natural convection occurs. Therefore, this factor will be modeled for the correlation of the models to take place.
In conclusion, through thermal analysis and testing, the team will endeavor to meet the challenging and unique requirements of the biological experiment inside the sealed vessel. As the mission progresses towards launch, it is hoped that it will offer valuable insights and lessons on how thermal control can be achieved and validated in subsequent biological missions and contribute to this burgeoning field of research.
Speakers: Mr Ioannis Psychias (Aristotle University of Thessaloniki/SpaceDot), Panagiotis Chatzigeorgiou (Aristotle University of Thessaloniki/SpaceDot), Mr Pavlos Vichas (Aristotle University of Thessaloniki/SpaceDot) -
4
Recursive Methodology for a flexible and responsive thermal analysis on a multimission 12U CubeSat Platform
Thermal analysis for CubeSats is a challenge caused by different factors. For instance, orbit parameters are not known until the very end of the development phase. On the other hand, thermal behaviour of a multimission platform can differ significantly from one mission to another. As part of the development of the CSUM's 12U platform, improvements to the thermal analysis process were required. Initially, we standardised the 12U model and, for recurring missions, identified the calculations needed to characterise the various behaviours, enabling us to build a database. As soon as we receive the customer's specifications, we select from the database a case close to the requested mission and obtain initial ideas for thermal control. The Thermal and Geometrical Mathematical models are adapted in the conventional way, by proposing thermal control solutions and repeating the calculation. In the event of unforeseen circumstances, the information in the database is consulted and the results of the preliminary simulations, which depend on the different trajectories and architectures, are exploited. As a result, the number of iterations required to size the Thermal Control System is greatly reduced. This approach allows us to increase productivity and reduce the risk of human error, a winning combination for thermal analysis.
Speakers: Juan Sebastian LONDONO PAEZ, Mr Pol ROUXEL -
5
DEEP SPACE CUBESATS THERMAL ANALYSIS AND CONTROL STRATEGIES
HENON (HEliospheric pioNeer for sOlar and interplanetary threats defeNce) and LUMIO (Lunar Meteoroid Impact Observer) missions are pioneering deep-space projects employing 12U CubeSat platforms. HENON aims to advance space weather forecasting by placing a CubeSat in a distant retrograde orbit (DRO) around the Earth, providing early warning signals for solar events. LUMIO, on the other hand, is designed to monitor the hidden side of the Moon from a halo orbit around the L2 point of the Earth-Moon system, detecting flashes from meteoroid impacts.
Though both missions face deep-space thermal environments, their unique characteristics pose distinct challenges.
HENON’s criticality lies in operating correctly at varying distances from the Sun (0.93 AU to 1.07 AU) and managing the presence of an electric thruster on board.
Meanwhile, LUMIO experiences fewer solar flux variations but will encounter eclipses during its operational life.
Both missions face high dissipation density coupled with limited volume and mass, making thermal system design particularly challenging and forcing thermal engineers to make use of operational constraints in combination with passive and active techniques. This presentation will outline the analysis process in the ESATAN-TMS 2023 environment and design choices made to address the environmental and operational scenarios of HENON and LUMIO. The thermal challenges, methodologies and solutions implemented will be discussed.
The presentation will conclude by offering insights into the workflow of next phases for both missions, highlighting the lessons learned and potential areas for improvement. The challenges faced and the solutions developed for HENON and LUMIO could provide valuable lessons for future deep-space CubeSat missions.Speakers: Daniele Cassano (Politecnico Di Torino), Francesco Latella (ARGOTEC S.R.L.)
-
3
-
Thermal Analysis Newton
Newton
Convener: Matthew Vaughan (ESA)-
6
Preliminary thermal decontamination study of Ariel
Atmospheric Remote-sensing Infrared Exoplanet Large-survey (Ariel) is the fourth medium-sized mission (M4) selected in the context of ESA's Cosmic Vision 2015-2025 programme and is scheduled for launch in 2029. Thermal control of the payload is based on a passive and active cooling approach. Passive cooling is achieved by a V-Groove shield system that takes advantage of the favourable thermal conditions of the L2 orbit to cool the telescope and the optical bench to stable temperatures <60 K. One instrument requires to operate below 42 K, which is achieved by an active cooling system based on a Neon Joule-Thomson cold end. To ensure the proper functionality of the mirrors, detectors and other optical equipment at operating temperature, an in-flight decontamination process will be performed to remove any thin ice films deposited on the critical optical surfaces of other surrounding elements. This study presents the preliminary results of the thermal study carried out to size the Ariel decontamination lines on ESATAN-TMS. Two scenarios have been considered, the first one, during the cool-down on the journey to L2, and the second one, a possible case of having to heat from cold (~60 K). In addition, since this type of analysis requires a considerable simulation time, the results in terms of heater duty cycle have been compared with the simulation time step, obtaining a trade-off between computational cost and accuracy.
Speaker: Mr ALEJANDRO Fernández-Soler (Universidad Politécnica de Madrid, Instituto Universitario de Microgravedad “Ignacio Da Riva” (IDR/UPM)) -
7
TOWARDS A THERMAL DIGITAL TWIN – Achievements, Challenges and Lessons Learned from a Thermal Analyst’s Perspective
The models used to analyse the thermal performance of spacecraft are complex, and characterise states and behaviours of a spacecraft for all subsystems and at various levels of abstraction. Configuring thermal models is historically a technical and time-intensive process, requiring intimate knowledge of the specific model and sub-models, as well as the spacecraft, its mission and the physics underpinning heat transfer. Towards a Thermal Digital Twin (TTDT) Project develops a new approach pioneered by ESA, Airbus, the University of Leicester and Epsyl that greatly enhances the power of spacecraft thermal analysis using the digital twin concept, applied to ESA’s Solar Orbiter spacecraft. Using modern computing frameworks, our approach containerises every aspect of the thermal analysis process, creates a direct link between in-flight telemetry and the model, and radically simplifies the configuration process used to set up and execute thermal analyses. This architecture is highly scalable, making powerful stochastic methods like Monte Carlo become practical for entire models and opening a path towards routine use of Reduced Order Modelling (ROM) for thermal analysis. A more thorough understanding of the design space reduces margins and increases vehicle performance, and the reduction in engineering time needed to perform analysis translates to reduced cost and more predictable project timelines.
TTDT was an 18 month project under the ESA GSTP Programme (Invitation to Tender AO/1-10605/21/NL/KML (Activity No. 1000030753 in the “esa-star” system)) to develop an existing advanced thermal model of a complete operational spacecraft and develop it as a Thermal Digital Twin (TDT) demonstrator software environment at Technology Readiness Level (TRL) 5.
This presentation comprises a summary of the achievements, challenges and lessons learned of the project from a thermal analyst’s perspective and also includes a summary of the developments road mapped to bring the TTDT to full industrialisation at TRL 6, Product Release.Speaker: Scott Morgan (Airbus Defence and Space UK) -
8
Arianespace Thermal Model specification for Thermal Coupled Load Analysis
In the frame of Arianespace mission analysis, thermal coupled loads analysis are needed to predict the thermal behavior of spacecraft on ground and during the flight. With the latest and upcoming launchers of VEGA-C and ARIANE 6 it was the occasion to update the technical specification for payload thermal models.
To introduce this new specification, a quick presentation of launcher (Ariane 6 and VEGA-C) thermal environment models will be presented: fairing external environment, convection under fairing, mobile gantry environment, cryo-tank conditions, aerothermal environment during the flight, plume effect. Then, explanations on how S/C thermal model is used in the coupled load analysis will be highlighted: GMM is used for radiative couplings (fairing, natural fluxes…), GMM is also used for convection couplings, power dissipation timeline. Finally, the Arianespace process to accept thermal model will be presented with the new features of the updated “Technical Specification”.
This new specification takes into account S/C manufacturer feedback (increase of maximum thermal nodes number, clarification of the deliverables …) and defines a new “thermal model by launcher” approach. With this new specification, S/C model delivery for thermal coupled loads analysis will be simplified and acceptance tests at launcher Prime level will be improved. As the Technical Specification is in line with thermal modeling standards, only evolutions and main features wrt. previous specification will be presented (e.g. new GMM accepted by launcher Prime, payloads stack configuration, max thermal nodes by S/C mass, thermo-optical properties).
Speaker: Guillaume DAVY
-
6
-
13:00
Lunch Break ESTEC Restaurant
ESTEC Restaurant
-
Lunar Night Survival Einstein
Einstein
Convener: Dr Philipp Hager (ESA)-
9
Modification of thermo-optical properties by lunar dust simulants - preliminary measurement results
This paper reports on the degradation of thermo-optical properties of materials used in thermal and power functional surfaces due to lunar dust. A large set of solar cell coverglasses (CVG), radiator coatings such as Optical Solar Reflectors (OSR), Second Surface Mirrors (SSM), or white paints, as well as MLI outer layers are tested after deposit of Lunar Dust Simulant (LDS).
The solar absorptance (alpha) and emissivity (epsilon) parameters are measured for different LDS deposit conditions. The approach proposed here is to accumulate dust with increasing levels of surface coverage (sub-monolayers of LDS with the coverage percentages from 5 to 30 %). The overall objective is to establish the law that governs the evolution of alpha or epsilon with LDS coverage. This evolution law can be plotted versus dust coverage in % or in µg/cm² (from mass measurement).
Then, a temperature investigation is also performed on a sub-set of materials (OSR, SSM and paintings).
The set-up used for dust deposit, thermo-optical measurements and specific test procedures will be described. The measurement test plan will be discussed accounting for the specific contraints linked to the measurement of LDS contaminated samples. Preliminary data on coverglasses, OSR and SSMs with LHS-1 deposit (LDS from Exolith Lab with custom sieve < 100 µm) will be disclosed showing the influence of LDS coverage level on the thermo-optical response of materials.Speaker: Sophie Duzellier (ONERA) -
10
Thermal modelling of polar lunar landing sites using the ESATAN-TMS Python API
This is a follow up to the presentation given at the ESTEW 2021, “Modelling of a polar lunar landing site ESATAN-TMS”. The focus of the presentation is on the thermal modelling of lunar South pole landing sites, with intermittent illumination conditions, applicable to upcoming ESA missions PROSPECT and Argonaut. For these, there is an interest to have a practical modelling of the lunar surface temperature, whilst maintaining a reasonable model size and computational time. Three lunar regolith thermal models with increasing complexity are evaluated with examples shown in ESATAN-TMS.
As a secondary topic, the presentation showcases three novel uses of the new ESATAN-TMS 2023 Python API. The API permits interaction with the model tree and access/modification of primitive attributes. The first example concerns meshing of the lunar surface, using Lunar Digital Elevation Model data and third party tool MeshLab for a given landing site. The second example demonstrates a connection between ESA SPICE service WebGeocalc to get vectors of azimuth and elevation of solar illumination of the lunar surface given and landing site location and epoch. Finally, the last example concerns the thermal model, and shows how a sub-surface regolith model can be applied onto a surface mesh via generation of properties, non-geometric nodes and conductors.
Finally, comparisons of modelling techniques will be drawn comparing terrain to the disk modelling. In addition, some conclusions about the ESATAN-TMS Python API are made, with some suggestions for the future improvements.
Speaker: Matthew Vaughan (ESA) -
11
Arquimea's solutions for Lunar night resilience
Night resilience is an important point in the thermal management of any vehicle in Lunar or Mars surfaces. Arquimea has thermal control hardware for high and low temperatures, and solutions to decouple sink from components, securing the functionality of the components inside the lunar vehicle. These solutions, with TRL9 in both heat pipes (HP) and Loop Heat Pipes (LHPs), required new proposals to achieve the high demanding requirements needed in a Lunar vehicle.
In this presentation, a trade-off of different proposals to deal with the dust and the different requirements of the Moon, if in pole or equator, will be presented, taking special attention to Lunar night resilience. Introducing the requirements necessary for the design of a LHP.
A brief review of the design requirements in the Lunar surface will be compared to the solution selected for ExoMars Rover Module (RM) thermal control, where Arquimea developed 4 units, 2 of them integrated on the Service Module (SVM) and two of them on the Analytical Laboratory Drawer (ALD). This development, now in TRL8, was composed by radiators and Propylene LHPs with a passive regulation valve. Each LHP is designed to transport up to 50 W and operate at temperatures from -50 ºC to +55 ºC at the evaporator level and from -120ºC to +55 ºC at the condenser, the decoupling of these different levels was made by Pressure Regulating Valves, providing protection at cold Martian night.
Speaker: Pedro Argente Hernández -
12
Heat transfer and heat storage: a combination of technologies for long-term survival on the Moon
Long lasting mission on the Moon both robotic and human are limited mainly by electricity and heat, with the first one used also extensively to produce heat. An efficient heat management, even better, completely passive is the key to enable these missions. Azimut Space explored and verified two technologies in this field.
The first one, developed with and in the frame of a mission for DLR, is a special type of completely passive diode heat pipe which reached TRL9 flying to space.
The second, developed with Walopt and CRM Group, is a heat storage device based on PCM developed for a Mars mission, of which performances were verified in thermal vacuum environment.Speaker: Luca Celotti (Azimut Space GmbH)
-
9
-
Thermal Control: Thermal control Newton
Newton
Convener: Dr Paolo Ruzza (ESA)-
13
Qualification and Applications of Phase Change Material (PCM) Heat Capacitors for Space Missions
PCM are materials selected for their high latent heat, which the phase transition (melting and solidifying) at the relevant temperature range is able to absorb and release a large amount of energy. They are usually stored in hermetically sealed container which is thermally coupled to the dissipative unit. Although already existing for a long time and used on several Space missions, PCM capacitors are still regarded as a potential and efficient thermal control solution, not only to cope with launch missions (including several engine re-ignitions, deorbitation), but also for orbiting spacecraft missions, for which thermal control PCM can be an asset. With the perspective of two foreseen flights (HEXAFLY and YPSat cubesat) and the potential use for LEO missions and planetary missions (lander or rover), PCM heat capacitors have recently completed qualification tests and characterisation thermal balance tests.
Speakers: Mr Nicolas Nutal (CRM Group), Romain PEYROU-LAUGA (ESA) -
14
GSE and characterization of a phase change material heat capacitor
Heat capacitors are often used in space application to control temperatures during high transient heat loads or alternating hot/cold periods. Due to their purpose, they are characterized by high thermal inertia. In addition, in order to lower their mass (with respect for example to a similar solution made out completely of metal), they can use materials, such as Phase Change Materials (PCMs), which allow storing and releasing heat via phase change. This causes additional issues in design, such as materials compatibility, durable sealing, and presence of low conductivity materials. In particular, melting/solidifying cycles as well as unit overall through conductance are critical parameters to assess the unit's performances and its usability in a system. These parameters shall be characterized with great precision and therefore specific test setups and procedure have been established in agreement with the client (AIRBUS UK) and ESA.
Speaker: Matvei Andreev (Azimut Space GmbH) -
15
Aerobraking for EnVision
Development of aerobraking MLI and deployable flaps
EnVision, the upcoming medium class mission to Venus, will implement an aerobraking maneuver in the upper Venus atmosphere, in order to decrease velocity and reach its final mission orbit. In addition to the body of the satellite, it is intended to use dedicated aerobraking flaps, as extensions of the solar array assembly. During breaking, the exterior of spacecraft and flaps will not only be subjected to aerothermal heat flux, but also to high concentrations of atomic oxygen (ATOX), which is known to strongly degrade materials.
In order to protect the satellite from these conditions, dedicated multi-layer insulation (MLI) will be required. The foreseen thermal conditions are already challenging, requiring high-temperature capable materials. While extensive heritage on MLI materials in high temperature environments is available, the combination with high ATOX fluence is unprecedeted for European missions. Many typical outer layer materials, such as Polyimides, are known to be not suitable in sustained ATOX environments. Thus, an investigation was done into a suitable lay-up.
Much of the focus of the investigation was on the outer layer materials, as it would be needed to sustain the ATOX flux and protect the inner layers. Candidate materials, including coated titanium and polyimide foils as well as glass fabric, were investigated regarding their high-temperature stability. The deciding test of this sample level test campaign was, however, a plasma wind tunnel test, combining ATOX exposure with heat flux.
Based on the findings of the sample level test campaign, a lay-up was selected from which a representative test specimen for a 3d calorimeter and cycling test was built. This breadboard was cycled more than 2000 times between -160°C and +350°C and its performance was evaluated 3 times; at beginning of life, mid of life and end of life. This was done in order to investigate a potential change in MLI performance over the lifetime.
The development of the aerobraking flap (incl. MLI and associated support structure) is currently ongoing. The design has been chosen such that it is highly scalable and compatible with different solar array models and configurations. For the drag surfaces, the same materials as for the spacecraft are foreseen. Preliminary mechanical and thermal analyses showed promising results. The hinges were identified as key components, depending on the solar array supplier, especially for thermal performance, as the unprotected hinges may introduce significant heat into the aerobraking flap assembly.
In this talk, the testing campaign for the MLI selection will be presented and the current design and status of the aerobraking flap will be discussed.Speaker: Christoph Roupec (Beyond Gravity Austria GmbH) -
16
Generic MLI Flap
Development of generic MLI flap for spacecraft interface ring
The launch vehicle adapter (LVA) is used to connect spacecraft to the launch vehicle. The spacecraft interface ring, which connects the S/C to the LVA, remains exposed after separation, when the spacecraft is released to its target orbit. The unprotected and exposed interface ring on the spacecraft represents thus a significant heat sink, depending on the orientation of the spacecraft. Additionally, this ring often has restrictive temperature limits, requiring heaters and/or careful orientation of the spacecraft in order to remain within these defined ranges. Unfortunately, due to the mechanical requirements of the LVA, coatings, in order to improve the thermo-optical properties, usually represent only a very limited option.
The goal of the ESA project “Development of generic MLI flap for spacecraft interface ring” is to overcome these challenges by developing a system that can cover the interface ring after spacecraft separation. Apart from covering the I/F ring with insulation, the main goals of the design are to be simple, passive, and scalable to different LVA ring diameters.
The design was also focusing on easy and late implementation of the flap system as well as minimum volume consumption to generate the least impact on S/C design. Different solutions were investigated over the course of the project, and a trade-off was done, ranking the options regarding their viability. In the end, a system mounted on the inside of the S/C interface ring was selected, with individual, pre-tensioned flaps which are retracted initially to not disturb spacecraft mating operations and launch. During separation, these flaps close passively and guided in alternating sequence once the spacecraft is separated. The flaps are equipped with MLI, which forms closed overlaps in the final position, offering a significant improvement in thermal performance when compared to the bare exposed I/F ring. The type of insulation needed can be adapted for a wide temperature and performance range allowing the MLI flap to be used for practically every spacecraft, if seen needed.
According to the design, a representative segment of the system has been built and tested regarding mechanical functionality, MLI coverage of the S/C I/F ring, compatibility with launch as well as shock loads and influence of thermal cycling on the system.
The selected design and current state of the testing campaign will be subject of this talk.Speaker: Mr Christian Ranzenberger-Stindl (Beyond Gravity Austria GmbH)
-
13
-
16:00
Coffee Break Einstein and Newton
Einstein and Newton
ESA/ESTEC
Keplerlaan 1 2201 AZ Noordwijk The Netherlands -
Thermal Design Newton
Newton
Convener: Moritz Branco-
17
CoCa - Thermal Design and Analysis of the Comet Camera
CoCa is visible light range imager onboard the Comet Interceptor spacecraft. Its objective is to provide color imaging of a comet, at a resolution sufficient to determine its structure and homogeneity. The launch is planned in 2029.
A brief introduction to the Comet Interceptor mission is presented, followed by a description of the CoCa thermal design.
The requirements to the CoCa thermal design are to stabilize the CMOS and the telescope’s structure at their design temperatures. Challenges are a wide range of S/C interface temperatures, limited heater power availability and potential Sun illumination.This presentation aims to provide a general overview of the CoCa instrument and a comprehensive description of its thermal design, analysis, and the future verification plan.
Speaker: Sebastian Wolf -
18
The Thermal Design of the Columbus Ka-band Terminal
The Columbus Ka band terminal (ColKa) is a communication system, currently installed outside the ISS, that connects the Columbus laboratory and the European Data Relay Satellite system. It enhanced the existing Columbus on-orbit and ground communication systems and created an additional bi-directional Ka band data transmission for the ISS.
The communications system electronics, provided by MDSRL (MDA UK), were accommodated on a platform developed by Kayser Italia, under ESA contract.
The terminal was launched February 15, 2020, onboard the NG-13. Afterwards, it was stored inside the ISS. Before being installed in its final positions, preliminary activities were performed inside the ISS releasing the Antenna locking features and mating the six cables. The terminal was then installed on January 2021 in its final position (outside the Columbus module) via an Extra Vehicular Activity (EVA) during the ISS spacewalk 69 by astronauts Victor Glover and Michael Hopkins. Kayser Italia provided support during this crucial phase.
The Columbus Ka band terminal is currently operating outside the ISS.The presentation describes of the Columbus Ka band terminal platform thermal design, while introducing also the main challenges encountered during the project.
In particular, ColKa contains a significant number of electronic units, some of which are characterized by narrow operating temperature ranges. Additionally, the power dissipated during the different operating phases can vary significantly. Moreover, since ColKa was installed via EVA, it needed to remain unpowered throughout the entire installation period.
Large radiators were employed to dissipate the substantial amount of heat generated during the most critical operating phases. Meanwhile, a passive heating system was implemented to maintain ColKa's functionality in cold conditions. Dedicated flight support equipment, such as temporary MLI covers, was provided for the installation phase.The thermal balance / thermal vacuum tests performed at the European Test Services facilities (in ESTEC) are also presented and discussed.
Speaker: Fabio Lorenzini (Kayser Italia S.r.l.) -
19
JUICE (JUpiter Icy Moon Explorer): 6 months in Space
JUICE - JUpiter ICy moons Explorer - is the first large-class mission in ESA's Cosmic Vision 2015-2025 programme. With its launch in April 2023 and the arrival at Jupiter in 2031, it will spend at least three years making detailed observations of the giant gaseous planet Jupiter and three of its largest moons, Ganymede, Callisto and Europa. The JUICE spacecraft carries the most powerful remote sensing, geophysical, and in situ payload complement ever flown to the outer Solar System.
JUICE spacecraft thermal control has to cope with a large variation of external environment during the mission (Sun flux from 3323 W/m² in the inner Solar System down to 46 W/m² in Jovian environment) and long eclipses of up to 4.9 hours. It is designed with the objective to minimize the impact of the external environment on the spacecraft through high efficiency Multi-Layer Insulation. Minimizing heating power demand especially during science and communication phases and minimizing hardware mass is a constant concern and solutions were found to build to a maximum extent a robust and passive thermal design supplemented by heaters.
The presentation will focus on the thermal performance of the spacecraft during its 6 first monts in Space, from LEOP and Near Earth Commissioning Phase to the early phase of the cruise to Jupiter.Speaker: Romain PEYROU-LAUGA (ESA)
-
17
-
Thermal Testing Einstein
Einstein
Convener: Andreas Mussger (ESA)-
20
Thermal Balance Test and Thermal Model Correlation of SMILE Satellite Payload Module
SMILE is a joint mission between the European Space Agency (ESA) and the Chinese Academy of Sciences (CAS). The mission is aimed to observe the interaction of the solar wind with the Earth magnetosphere by simultaneous X-ray imaging of the magnetosheath combined with UV imaging of the northern aurora. ESA will be in charge of the Payload Module, while the Service and the Propulsion Module is provided by CAS. This presentation is aimed to describe the SMILE PLM thermal validation and verification strategy. In particular, it is focused on the PLM STM test campaign conducted at the European Test Services (ETS) facilities in 2022 and the associated correlation exercise. The presentation covers the test set-up definition, test execution and the thermal model correlation. In addition, it is provided a brief description of the upcoming PFM thermal validation and verification campaign.
Speaker: José María García Garrido (Airbus) -
21
Mars Sample Return – Sample Fetch Rover – Gas Insulation Design and Test Definition
The Sample Fetch Rover (SFR) was a key element of the Mars Sample Return program, having the objective to locate, retrieve and return samples cached by the Mars 2020 (Perseverance) Rover. Designed for autonomous operations and fast mobility on Mars terrains, the Sample Fetch Rover mission profile included traverse to the “depot” where Perseverance will have left the tubes containing soil and rock samples; collection and on-board storage of the tubes, and their transport back to the Mars Ascent System. A key design driver for SFR, as with any Martian mission, is keeping equipment warm during the cold Martian night, with environmental temperatures dropping to -130°C. SFR does not have any form of radioactive heating and relies entirely on electrical heating to sustain internal temperatures. As such, heat leaks to the cold environment must be minimised, with the main heat leak being via the CO2 atmosphere. This imposed a need for an efficient gas insulation design around hot zones within SFR. To achieve this a literature review of previous Martian gas testing was conducted, identifying key parameters for a gas insulation design such as maximum gap size which suppresses convection. From this multiple designs for novel gas insulation solutions for SFR were created and a test was defined to determine empirically which design provides the highest level of insulation. This paper details the literature review, the various novel gas insulation designs and the proposed testing for design selection.
Speaker: Arthur Dunlop (Airbus Defence & Space UK) -
22
EarthCARE TB/TV Test in the LSS
The EarthCARE satellite TB/TV test was performed in the Large Space Simulator facility (LSS) at ESTEC, in the period of January 26th, to February 9th, 2023.
The test objectives, the test phases and the requirements for the test environment led to a test setup with an active cooling system for the ATLID PLH’s and a cavity for the CPR main reflector. The test set-up including cooling loop and the facility interfaces are shown in detail. A short discussion on test phases and results follows. Simplification of test flow and the test set-up is also discussed.
Finally, lessons learnt for future testing of large satellites are outlined.Speaker: Aydin Cataloglu (Airbus)
-
20
-
18:00
Cocktail Foyer or Wintergarden
Foyer or Wintergarden
-
08:30
-
-
Lunar generic Newton
Newton
Convener: Alexandre Darrau (ESA)-
23
Lunar Surface Simulation Methodology for Thermal Analyses on Moving Surface Objects
In this contribution, the concept of a thermal simulation environment for moving objects on the lunar surface is presented. The goal of this thermal simulation environment is to enable the reliable calculation of the temperature behaviour of a given object on the lunar surface by providing the respective transient heat fluxes for a mission on a given travel path.
At first, the modelling concept for a part of the lunar surface is presented. The relevant lunar topography is imported with data from NASA’s SLDEM2015 model and further processed, in order to obtain a three-dimensional thermal model of the relevant surface cut-out according to the defined travel path. In subsurface direction, the model consists of multiple nodes within a lunar dust layer and a regolith layer to depict the thermal behaviour.
The geometry of the object to be analyzed is placed onto the lunar surface at the desired coordinates and oriented according to the topography. The object is moved across the lunar surface as defined, and its orientation is adapted for each new time step depending on the topography underneath.
Additional to the lunar surface model, the concept of how the radiative cases are set up, updated and evaluated is introduced.
In the end, a whole example simulation result shall be presented.Speaker: Joel Guetzlaff (FH Aachen University of Applied Sciences) -
24
Thermal analysis of a student developed micro-rover
In the quest for planetary exploration, rovers have played a pivotal role in gathering crucial data and expanding our understanding of the planetary surfaces. Currently, due to the active participation of the ESA in NASA’s Artemis program, the European space industry is actively developing technologies for lunar surface exploration such as robotic rovers.
In this context, TU Delft’s Zebro student team is developing a six-legged micro lunar rover, which utilizes an innovative locomotion system based on six C-shaped legs. Zebro’s rover is planned to be deployed in swarms to help astronauts and bigger robotic rovers. The rover is the size of a shoe box, which allows to minimize launch costs and the inclusion in potential rideshare programs.
However, miniaturization also comes with challenges, especially related to rigid weight constraints. The rover is currently going through its second design iteration, approaching the first development test phase. The focus of this study is the thermal analysis and design iteration performed to meet the rover survivability requirements. The requirements have been tailored to the first mission: a technology demonstration where the rover will perform radiation measurements on the Moon surface.
The rover behaviour has been simulated in three different operational scenarios in the harsh Moon polar environment. The results have been used to improve the thermal control system to obtain a sturdy and reliable design. The thermal analysis has been performed in ESATAN-TMS.
Based on the thermal analysis results, the Zebro’s thermal design was modified using commercial off-the-shelf components, striving to meet the strict mass, power, volume, software, and budget constraints of the project. The design iteration includes changes regarding the insulation systems, the introduction of a radiator, and the use of thermal straps to better spread the internally generated heat. The design changes were verified numerically with ESATAN-TMS and will be validated in the upcoming test campaign.
The results point to an improved thermal design that makes the overall Zebro solution more robust and efficient. The results presented also add to the practical understanding of the difficulties associated with maintaining thermal control in miniaturized space structures.Speakers: Ines Uriol Balbin (Delft University of Technology), Riccardo Brambilla (TU Delft, Lunar Zebro) -
25
Development and testing of the Active Thermal Switch (ATS)
With the growing interest in lunar missions during the last few years, the demand for technologies which allow hardware to survive the extreme conditions of the lunar night has increased. One promising approach is to enable high performance bi-directional thermal control in space applications.
Lunar Outpost EU has developed and tested an active thermal switch for this purpose. The device allows to actively change the thermal conductance between a heat source and a heat sink from a low to a high value. The thermal switch was tested in April 2023 and a new design iteration deduced based on the test results.
To describe system performance more accurately, a new method of calculating Turn Down Ratio (TDR) is being used to assess the performance of the switch in a representative environment.
Speaker: Tobias Flecht (LunarOutpost EU)
-
23
-
Thermo-Elastic Einstein
Einstein
Convener: Dr Paolo Ruzza (ESA)-
26
Advances in Thermoelastic Analysis Avoiding The Need of a Finer-Grained Thermal Model
Today, thermoelastic treatment relies on providing maps of average temperatures by zone. This is a conservative approach because these temperatures gradients are maximized. The main objective is to develop an automated link between mechanical engineering models and thermal analysis ones, with different methods (finite elements vs nodal method) and significative geometrical representativeness differences (100000 vertices vs 1000 nodes).
One of the main challenge consists in having a precise enough thermal model in order to obtain satisfying temperatures at mechanical points in order to compute the thermoelastic deformation of the structure and depointing of the instruments.This operation while being coarse enough to perform simulation in an acceptable amount of time.
If the initial thermal model is not accurate enough, the tedious task of designing a more accurate one usually has to be performed. To tackle this issue, DOREA and TAS investigated the idea of determining temperatures at mechanical points from an existing e-Therm thermal model without the need of redesigning a finer-grained thermal model.
Thanks to e-Therm algorithms, especially for instrumented panels, e-Therm allows a detailed temperatures cartography to be a physical representation of the heat equation (without any interpolation or extrapolation algorithms).
For the remaining parts of the thermal models and for all mechanical geometrical parts which don’t have a thermal representativeness, we apply an interpolation/extrapolation method.
The method is currently being tested and validated on the complete EUTELSAT 10B satellite. E10B telecom program provided a detailed temperatures cartography which match directly on a FE mechanical model declined over time. This tool may also be used to determine the worth sizing cases for thermoelastic aspects.Speaker: Mx Wayne CROISETU (Dorea) -
27
European Guidelines for Thermo-Elastic Verification
Almost every Scientific and Earth Observation mission is faced with the need for thermo-elastic verification.
The European Space community has been, despite all previous activities to date, lacking commonly accepted guidelines for performing the end-to-end thermo-elastic verification.
To solve this issue, ESA emitted an invitation to tender, in 2020, to the European Community to work for European Methods for Thermo-Elastic Verification (briefly TEV). This project was aiming at supporting the European space community to establish Europe wide accepted and validated methods for thermo-elastic verification and at consolidating these in guidelines.
From 2021 till this year 2023, a consortium of the core partners Thales Alenia Space France and Italia, ATG Europe BV and OHB system AG has worked on the TEV project under ESA contract. The main achievement of the project is a thermo-elastic verification approach that has been established with the contribution of the members of the European Working Group on Thermo-Elastics. This verification approach is the main subject of the presentation.Speaker: Simon Appel (ATG Europe for ESA)
-
26
-
Thermal Design Einstein
Einstein
Convener: Dr Paolo Ruzza (ESA)-
28
Space Nuclear Propulsion: Overview and challenges
An overview of the nuclear propulsion for space applications will be presented with a particular focus on thermal challenges. Both Nuclear thermal Propulsion and Nuclear Electric Propulsion will be detailed also providing few concepts for future missions and technical thermal challenges to be overcome to reach mission readiness.
Speaker: Mr emmanuel caplanne (ESA)
-
28
-
10:30
Coffee Break Einstein and Newton
Einstein and Newton
ESA/ESTEC
Keplerlaan 1 2201 AZ Noordwijk The Netherlands -
Thermal Analysis Newton
Newton
Convener: James Etchells-
29
ANSYS Icepak CubeSat Thermal Models Correlation
It is common for CubeSat missions to use simplified analysis models, leveraging software suites which are tuned for thermal analysis with coarse mechanical and power dissipation models of spacecraft components. The inherent non-linearity of thermal simulations and the complexity of typical boundary conditions for realistic satellite components often result in this trade-off and reduction in the simulations’ fidelity.
Even though it is not specifically tailored for space-domain simulations, ANSYS Icepak provides a much more detailed PCB and component thermal model which can lead to significantly improved fidelity. EnduroSat has developed a strategy for modelling the LEO environment experienced by a satellite by applying determinate fluid settings inside the calculation domain (cabinet) and imposing realistic boundary conditions exported from a proprietary software. This software uses the NRLMISE-00 atmospheric model and accounts for surface optical properties, producing as output the Sun, Earth IR and Albedo fluxes impacting on each exposed surface of the spacecraft.
The benefits of this strategy is the capacity to readily import ECAD files of PCBs, of both subsystems and solar panels, define dissipations on the level of EEE components and obtain very precise thermal map throughout the satellite components.
In the present work, we outline the methodology and compare the numerical results obtained through ANSYS Icepak with those measured from orbit by one of EnduroSat's satellites. It is shown that about 5 orbital periods are sufficient to reach a steady-state temperature trend for all points of interest given the particular mesh settings and satellite properties. The accuracy obtained is better than 5 degrees after fine-tuning of parameters which are not directly measurable.
Apart from fidelity, the ECAD import feature of ANSYS allows for a detailed analysis of specific electronic components, which may require a specific vias pattern to dissipate their waste heat, allowing then for the hardware engineers to have direct feedback on their PCBs thermal design in a much finer detail.Speaker: Alessandro D'Anniballe -
30
Thermal Analyses of Greenhouse to Support Crewed Lunar Habitation
Humanity is tackling the challenge of creating a permanent human presence on the Moon, and Canada is contributing by funding novel ideas for Moon infrastructure. With support from the Canadian Space Agency under the Lunar Surface Exploration Initiative, Canadian companies are actively developing solutions to explore and stay for extended periods on our planet’s satellite.
Under this initiative, Canadensys and MayaHTT recently completed a Phase 0 study for a greenhouse to support crewed lunar habitation. This pressurized module, with a mass budget of 11,000 kg and a nuclear reactor for power production, will be landed near a habitat to demonstrate food production on the lunar surface. The objective of this initial phase was to develop and size the architecture for the Thermal Control System.
To obtain insight on the driving design parameters, Maya developed a combined thermal and flow model. A detailed CFD representation was used for the inside of the module, allowing to capture the flow velocities, heat transfer coefficients, as well as verifying temperature and humidity in the plant enclosures and the rest of the habitat. A simplified thermal representation was used for the outside of the module, to capture conduction between the different parts and radiative heating and heat exchanges on the Moon’s South pole.
This presentation will show the thermal and flow results from this Phase 0 study, and discuss the future work and development required in the following phases.
Speaker: Jean-Francois Labrecque (MayaHTT) -
31
Thermal mathematical model validation by tests performed in TVAC
OBJECTIVE: The role of the Thermal mathematical model is to help in the design of the spacecraft Thermal Control System. Temperature uncertainty must be decreased as much as possible and kept under control, to achieve this whole process must be well thought-out especially validating thermal model via TVAC test. The purpose of this study was to determine steps and measures that allow us to control uncertainty and gain trust in analytical results.
METHODS: The process was analysed for key factors that influence temperature distribution both in mathematical model and during physical tests. Those factors had to be well described, their influence estimated. Each step during the tests was designed to provide the data output that allows for easiest and most reliable correlation with the mathematical model. Mathematical methods and success criteria had to be established for correlation.
RESULTS: Uncertainty temperature margins were established, step by step process has been worked out. Data stets have been created, correlation between test data and analytical model done, differences compared, discussed, and justified. Design loop will be changed to include conclusions from test, processes will be refined.
CONCLUSIONS: Controlling processes that maintain lots of variables imposes strict, well considered steps to achieve method that generates trustworthy results from mathematical models. Such methods allow to decrease development time and achieve higher precision in Thermal Control Systems.
Speaker: Michal Alaszkiewicz (Institute of Aviation) -
32
From Manual to Automated: Optimizing Spacecraft Thermal Modelling Processes with AI
Traditional spacecraft thermal modelling processes can be costly and time-consuming due to manual effort required by engineers to build and update thermal models. Recent advancements in AI and machine learning have enabled automation of many thermal engineering tasks including geometry construction, model reduction, mesh creation, etc. In this technical presentation, we will showcase the progress made in automating spacecraft thermal modelling processes through a real-world example: the Copernicus CO2M Ka-Band Downlink Antenna System.
Our presentation will demonstrate how automation has decreased the time and resources required to create thermal models, leading to more optimized thermal control system designs. We will also outline a roadmap towards near-full automation of spacecraft thermal modelling processes. By minimizing manual intervention, we can further optimize the design and performance of spacecraft thermal control systems.
Our work presents a unique application of state-of-the-art AI and machine learning algorithms that specifically target the challenges faced by spacecraft thermal engineers. By utilizing these algorithms, we can automate tedious and repetitive tasks such as geometry construction, model reduction, mesh creation, and more. This enables engineers to focus on more complex and creative problem-solving, leading to more efficient and effective spacecraft designs. Our approach represents a significant departure from traditional spacecraft thermal modelling processes and has the potential to revolutionize the field.
Our presentation will showcase the benefits of using AI and machine learning to automate thermal modelling tasks. Specifically, we will demonstrate the significant reduction in time and resources required to create thermal models, leading to more optimized thermal control system designs. We will also provide a roadmap towards near-full automation of spacecraft thermal modelling processes, highlighting the potential benefits of further minimizing manual intervention.
The work presented in this abstract is in development, with preliminary results achieved through prototypes. Our roadmap towards near-full automation of spacecraft thermal modelling processes is a concept, with ongoing development and testing.
By attending this presentation, participants will learn the latest techniques for automating thermal modelling tasks, as well as best practices for integrating these technologies into their own thermal engineering workflows. The potential benefits of this work include improved efficiency and effectiveness in spacecraft design, as well as a reduction in manual effort required by thermal engineers.Speakers: Ted Pyne (Nitrexo), Yannick Melameka
-
29
-
Thermal Design Einstein
Einstein
Convener: Marc Broussely (ESA)-
33
CNES Flight Experiment for Thermal Coatings Aging: THERME
The in-flight evolution of thermo-optical properties of thermal coatings is of great concern when defining the thermal control system (TCS) of spacecraft. Experience (in-flight measurements and aging tests in laboratory) demonstrates that the parameter really affected by the in-orbit aging is the solar absorptivity, which often increases when coatings are under space environment conditions. To define spacecraft TCS, thermal engineers have to take into account, from beginning of life (BOL) to end of life (EOL), the thermo-optical properties evolutions of the external coatings they intend to use (the solar absorptivity and the emissivity). Radiative surfaces sizes cope with the hottest conditions of the mission, which generally depend on the EOL properties of external coatings. But the larger the surfaces, the higher the heating power needed for the coldest conditions of the mission, which generally depend on BOL properties. Improving the knowledge of the in-orbit evolutions of the solar absorptivity of thermal coatings is consequently of paramount importance to optimize the TCS designs, and then to better master the on-board heating power consumption.
In this context, CNES has developed since 1990 a very simple and low cost experiment, called “THERME”, to evaluate the degradation of space coatings in real orbital conditions. This experiment was previously carried on low Earth orbit (LEO) spacecraft such as SPOT 2 and 5, HELIOS 2A and 2B and Demeter, all removed from operational service. In the last few years, the THERME experiment design was extended for geostationary (GEO) mission typical constraints and is now flying on ATHENA-FIDUS and KOREASAT from TAS and on a telecom mission from ADS.During the European Space Thermal Engineering Workshop 2023, we present the overall concept and design of THERME, the qualification logic and the test campaign. We discuss also in methodology for exploitation of flight results of THERME, of main flight results and we identify the axes of improvement for future missions.
Speaker: Simona Calarco (CNES) -
34
Envision mission: Presentation & derisking activities
The ESA EnVision will determine the nature and current state of Venus' geological evolution and its relationship with the atmosphere, to understand how and why Venus and Earth evolved so differently.Perched at the inner edge of the habitable zone, Venus may once have been habitable, with liquid water oceans, before developing the enormous greenhouse warming which renders it uninhabitable today, thus providing a natural laboratory for studying the evolution of habitability. Venus is essential for understanding the links between planetary geophysical evolution and habitability of terrestrial planets from our own Earth to terrestrial planets and exoplanets everywhere.The Envision mission will develop an holistic approach performing high resolution radar mapping from the crust and mantle to atmospheric studies, at both large and regional scales.The spacecraft and its instruments thermal design will be presented, pointing out thermal challenges induced by such a mission. Test activities carried-out at material level to specifically answer the aerobraking phase will be also presented.
Speaker: Mr emmanuel caplanne (ESA) -
35
3MI Heat Pipes and Radiators assembly: design, manufacturing, verification and testing challenges
Arquimea Space recently developed a Heat Pipes and Radiators Assembly (HPRA) for the 3MI Instrument (Leonardo S.p.A., Campi Bisenzio site) onboard MetOp SG satellite (Airbus DS, ESA).
Arquimea Space was in charge of the design, manufacturing, verification and testing of this HPRA, following the corresponding specifications from The Leonardo Company. Six models have been produced and delivered (STM, QM, FM1, FM2, FM3 and FS) along the six years this project took place.
This HPRA comprises five radiators working at different temperature levels, ethane HPs, ammonia HPs, a supporting structure, a sunshield, insulation (MLI, SLI, washers), electrical parts (heaters, thermistors, thermostats) and titanium brackets and isostatics. Two of the radiators were small independent subassemblies that included a radiator, heat pipes, electrical parts and insulation.
This HPRA turned out to be an important engineering, production and testing challenge, given the demanding performances required to this assembly, both thermal (temperature levels, gradients and insulation) and mechanical (stiffness, vibration levels, thermoelastic loads). To remark one of the radiators and the corresponding HP operate at very low temperatures (around -100ºC), while the rest operate at more usual minimum temperature levels (-40ºC/-5ºC). Besides, the HPRA is very compact. All the hardware is practically contained in an envelope 1mx0,5mx,0,65m (excluding part of the ammonia HP, the most protruding items). In particular, the gap between the coldest radiator and the supporting structure is less than 10 mm. This narrow gap turned out to be a very stringent design driver for the overall system, specially the insulation. The HPRA models underwent several demanding thermal and mechanical test campaigns (including vacuum testing, thermal cycling and bake-out) to demonstrate their capabilities.Speaker: Jose Luis Pastor -
36
Thermal Control Design and Challenges for CIMR
The Copernicus Imaging Microwave Radiometer (CIMR) is part of ESA’s Sentinel Expansion missions and is a complex system involving a satellite platform, a rotating microwave radiometer and a deployable mesh reflector. The purpose of the mission is to monitor and provide information on Earth’s water surfaces, by gathering radiometric data on sea surface temperature, sea-ice concentration and salinity percentage. This presentation aims to introduce the system’s thermal control: its design drivers, challenges and technical solutions.
CIMR is currently advancing to the CDR phase, foreseen for the last quarter of 2025. Due to the complex interface system between payloads and instruments, an avant-garde thermal management is required, consisting of both active and passive thermal control means. Part of the thermal challenges include: an environment definition for the rotating scan mechanism, the thermal behavior of the reflector mesh, the behavior of heat pipes under centrifugal forces and the thermal interface management within the platform. A set of hybrid thermal models were assembled to approach such challenges, consisting of both detailed and correlated reduced sub-models. In addition, a considerable effort was devoted to the thermal management of the satellite’s interfaces between platform, radiometer and reflector.
Thermal control trade-offs are currently in progress and the final design will include heritage thermal hardware as well as a few tailored items to meet specific requirements. It is foreseen that the final thermal control design will serve as heritage for future Earth observation missions involving large rotating payloads and deployable systems.Speakers: Matteo Chiappi (TAS-I), Dr Alberto Franzoso (OHB-I)
-
33
-
13:00
Lunch Break ESTEC Restaurant
ESTEC Restaurant
-
Heat Transport: 2-Phase Newton
Newton
Convener: Paula Prado Montes-
37
In Orbit Demonstrator for LHP² and AG190
For all its satellites, Airbus Defence and Space relies on top-level technology to implement the Thermal Control System. This Thermal Control System shall ensure that payload and/or equipment heat dissipation is transported and spread onto the S/C cold sinks (radiators) efficiently enough to maintain temperatures in the allowable ranges.
For this duty, some of the most advanced thermo-fluidic components available on the market are the AG190 Heat pipe (HP) and dual-core Loop Heat Pipe (LHP²) designed and produced by EHP.
Both these two products present very high performance for a very affordable price. However, their accurate capabilities, like the upper heat transport limit at very high temperatures, are not well determined, since on ground testing is influencing these figures due to gravity.For such thermo-fluidic components, only in-orbit testing can be considered as reliable. Therefore, EHP and Airbus Defence and Space have jointly designed, produced and tested in orbit a demonstrator carrying one AG190 and one dual-core LHP². This experiment has allowed to perform accurate performance mapping & determination of operating limits over a range of temperatures & powers for both products.
The presentation will report this joint activity and describe the main outcomes of the experiment.
Speakers: Mr John Ponsy (Airbus Defence and Space), Mikael Mohaupt (Design Engineer at EHP) -
38
Development of a vapour chamber in additive manufacturing for LEO active antennas. Trade-off and preliminary design
Latest generation of active antennas designs are demanding low thermal gradients and low volume (specially for LEO designs). Additive manufacturing introduces high flexibility to fulfil these main requirements, the 2-phase thermal component can be directly manufactured in the system to refrigerate, improving the thermal behaviour and increasing the level of integration in the system.
A trade-off for an active antenna refrigeration is presented, introducing the different TMM and processes required to validate the design. Different designs and coupons are presented in order to validate future works in the development of this vapour chamber design.
Speaker: Pedro Argente Hernández -
39
JAXA Two-phase Heat Transport Technology Development Overview
This presentation describes current status and future prospect of R&D activities on two-phase heat transport technology of Japan Aerospace Exploration Agency (JAXA). In addition to passive thermal control devices such as a loop heat pipe (LHP) and an oscillating heat pipe (OHP), R&D activities of active thermal control devices such as two-phase mechanical pumped loop are conducted. Active thermal control devices are expected to construct the innovative thermal control system for high heat-dissipation satellites and components or scientific instruments requiring precise temperature control. The overview of R&D activities related to two-phase mechanical pumped loop is also introduced in this presentation.
Speaker: Atsushi Okamoto (JAXA) -
40
GEO Telecom Satellite Thermal Control System: Hardware and development outline for a high power removal and transport system
Arquimea Space recently developed a thermal control system (TCS) that removes and transport high power levels (up to 6 kW) from the active antennae DRA (Airbus D&S-Spain) on board GEO Telecom Satellite satellites (Airbus D&S-France, Hisdesat, ESA). This TCS was defined after a coengineering phase with Aribus D&S Spain. Then, Arquimea Space carried out the detailed design, manufacturing and acceptance testing of the hardware that comprises this TCS.
This TCS comprises several pieces of hardware that work jointly:
• Heat pipes that collect the heat waste from antenna electronics. Given that the tight DRA internal volume, there HP are integrated along with the antenna electronics to be cooled as part of the antenna.
• Heat Pipes and Loop Heat Pipes that transport the heat from the HP that collect the antenna electronics heat waste and transport it to the main spacecraft radiator panels.Hardware MAIT activities were complex given its features and particularities. This was especially challenging for the LHP Sub-Assemblies (LSA) that its tubing goes all the along the spacecraft structure from the antennae to the spacecraft main radiator panels. These LSA were assembled and tested in full in-fight configuration in spacecraft like size GSE.
All the hardware underwent an exhaustive qualification test campaign to meet the specific requirements for GEO Telecom Satellite. Additionally, flight hardware undergoes acceptance both at component and assembly levels.
The hardware for PFM satellite has been already delivered to Airbus D&S-France. The next step is the production and delivery of the hardware for FM2 satellite.
Speaker: Jose Luis Pastor
-
37
-
Thermal Testing Einstein
Einstein
Convener: Romain PEYROU-LAUGA (ESA)-
41
Airbus Defence & Space Solution for TVAC tests data supervision : DynaThermaNeo
Space simulation in Thermal Vacuum Chambers is one of the major tests performed for Spacecraft qualification.
During these tests, huge amount (several thousands) of parameters need to be acquired for near real time real supervision or post-test analysis.
These parameters can come from :
-
The test facility such as the command control data
-
The instrumentation on test such as the thermocouples used for the qualification
-
The Spacecraft telemetries which are running also during the test
-
Other sources of data such as simulations, test rigs, gas analyser, …
To aggregate these data and be able to deliver them to the different stakeholders of the test (test operators, satellite architects and analysts, remote customers), Airbus Defence & Space developed DynaThermaNeo solution.
DynaThermaNeo ensures the test preparation, piloting interface and near real-time acquisition. DynaThermaNeo solution is based on DynaWorks software platform developed by Airbus Defence & Space and used in-house and by external customers in Aerospace and Defence industries.
The main objectives (and stakes) of the solution are :
-
Improve process efficiency --> test cost reduction
-
Develop flexible interfaces and configurations (open solution) --> adaptability and durability
-
Develop an user friendly user interface --> training time reduction
-
Be compliant with network constraints and test means
-
Reliability on critical systems
Speaker: Cédric LAURENT -
-
42
Conquering the Cold: Thermal Testing of MMX Rover IDEFIX's Locomotion Subsystem for the Exploration on Phobos
The Martian Moon eXploration (MMX) mission, led by the Japan Aerospace Exploration Agency (JAXA), is scheduled for launch in 2024 with the objective of sample-return from the Martian Moon Phobos and additional scientific observations of Deimos. As part of this mission, the MMX rover 'IDEFIX', developed collaboratively by the French Centre National d'Études Spatiales (CNES) and the German Aerospace Center (DLR), will serve as a mobile scout on the surface of Phobos. With its four-wheeled design and a weight of 25 kg, the rover will operate in microgravity and conducting in-situ measurements in areas of scientific interest.
The locomotion subsystem (LSS) of the MMX rover, developed, build and qualified by DLR's Robotics and Mechatronics Center, plays a key role in fulfilling the mission objectives. The LSS is designed to accomplish various high-level requirements, including the correct reorientation (so-called uprighting) of the rover after ballistic landing, precise alignment of the solar cells for optimal power generation, and the provision of different driving modes to explore Phobos and interact with its surface. Additionally, the LSS allows for adjusting the rover's ground distance to allow measurements with the Raman spectrometer.
To ensure the LSS can withstand the challenging conditions of the MMX mission, particularly the harsh environment during the cruise phase and the expected extremely low temperatures on Phobos, a comprehensive thermal design was developed. The LSS was subsequently subjected to rigorous testing throughout the development phases. The testing involved evaluating the mechanical, electrical and thermal aspects of various subunits, including the complex hold-down and release mechanism (HDRM), as well as conducting full functionality tests of the flight representative LSS during the qualification and acceptance stages.
This presentation provides an overview of DLR's approach to thermal testing activities for the LSS during the development phase of the MMX rover. It offers insights into the MMX mission as a whole and presents a detailed examination of the qualification and acceptance thermal tests conducted for the LSS, emphasizing the significance of these tests in ensuring the successful operation of the rover during the mission.
Speaker: Ralph Bayer (German Aerospace Center (DLR e.V.)) -
43
Thermal Balance Test Correlation of a SAR Antenna Segment considering two different Radiator Coating Approaches
This study presents a comprehensive investigation of the thermal balance characteristics and model correlation of a radar panel sample from ROSE-L (Copernicus SAR Instrument), incorporating the usage of high dissipative electronic units and featuring two distinct optical coating variants for the radiative antenna front.
The study aims to assess the thermal performance of the radar panel under realistic environmental conditions and to establish an accurate correlation between the physical prototype and the numerical model.
The thermal balance test was conducted in a controlled environmental chamber. Controlled thermal loads are applied to simulate various scenarios of the heat dissipation of its electronic units. Two different optical coating variants were applied on the antenna front to explore their influence on the panel’s thermal behavior.The numerical model incorporates all relevant material properties and a detailed layer structure. The model was validated against the experimental data obtained from the thermal balance test, ensuring its accuracy in predicting the panel’s thermal performance.
The results of the thermal balance test reveal valuable insights into the panel’s temperature distribution, highlighting the impact of the high dissipative electronic units on the overall thermal behavior.Key aspects of the thermal performance are:
- The through conductivity of the RF radiator structure which provides the thermal path between dissipating Front-End Components and heat rejection radiator and
- The heat rejection capability of the radiator front side mainly influenced by the thermo-optical properties of the radiator surface
A comparative analysis of the two available optical coating variants demonstrates their distinct heat absorption and radiation characteristics, thus providing essential guidelines for optimizing the radiative antenna front’s thermal properties.
The model correlation analysis demonstrates a satisfactory agreement between the numerical predictions and experimental measurements, confirming the reliability and accuracy of the thermal simulation framework.In conclusion, this study contributes to a better understanding of the thermal behavior of the ROSE-L radar panel. The results provide essential insights for enhancing the thermal management strategies of such systems and facilitating their integration into complex operational environments.
Speaker: Anja Huchler -
44
Design and Implementation of GSE for Cryogenic Thermal Vacuum Testing
Spacecraft components that are exposed to deep space often require testing at the cryogenic temperature levels they will sustain during the mission. To that end, a test facility not only requires a chamber capable of reaching high vacuum levels, but also the means of reaching temperatures below that of liquid nitrogen.
Moreover, this paper describes the design and implementation of mechanical and electrical ground support equipment by using a cryocooling unit and several other components to perform thermal cycling and conductance test campaigns of in-House-developed thermal hardware products.
The resulting system consisting of structural supports, as well as hardware and software for thermal control and monitoring, has successfully enabled measuring the conductance of custom-designed thermal straps at different temperatures, as well as subjecting them to thermal vacuum cycling between 40 and 350 K.Speaker: Mr Sebastian Ospina (Azimut Space GmbH)
-
41
-
16:00
Coffee Break Einstein and Newton
Einstein and Newton
ESA/ESTEC
Keplerlaan 1 2201 AZ Noordwijk The Netherlands -
Thermal Analysis Einstein
Einstein
Convener: Matthew Vaughan (ESA)-
45
Accelerating Radiative Heat Transfer Analysis for Space Systems using GPU-Based Ray Tracing
Thermal analysis for space systems encounters a significant bottleneck in computing radiative heating contributions to the heat transfer problem, particularly when transparent and specular materials come into play. In this study, we introduce an innovative implementation that harnesses the remarkable parallel processing capabilities of ray tracing on Graphical Display Units (GPUs). Specifically designed for NVIDIA GPUs, our implementation efficiently handles parallel view factor and/or direct radiative heating calculations through Monte Carlo ray tracing.
In a previous study, we demonstrated that our GPU-based algorithm exhibited extraordinary speed gains compared to the CPU implementation in Simcenter 3D Thermal-Multiphysics, specifically for surface-to-surface enclosure radiation. In this presentation, we extend the application of our GPU-accelerated methods to encompass Solar and Orbital heating radiation calculations. By comparing the computation times and accuracy of our legacy CPU methods with our new GPU techniques, we reveal the advantages of our approach for Solar and Orbital heating analyses. For the Solar heating functionality, we will be looking at a detailed lunar surface model based on LRO topology data that was constructed for the Canadien Lunar Rover mission. For the orbital heating mission, we will focus on a satellite model including articulating components.
Speaker: Florian Sanchez (MayaHTT) -
46
Radiative Exchange Factor Calculations Using New GPU Hardware-accelerated Ray Tracing Capabilities
This work presents a new implementation of the radiative exchange factors calculations for 3D geometry using Graphics Processing Units (GPUs) with hardware-accelerated ray tracing capabilities.
Radiative exchange factors (REFs) represent the overall exchange of thermal radiation energy between two surfaces. Although there are analytical solutions for particular geometric configurations, in practice REFs are computed using numerical methods. One common approach involves employing Monte Carlo ray tracing algorithms. In a Monte Carlo ray tracing process, the electromagnetic energy emitted by the surfaces is divided into discrete rays with an associated energy. Then, each ray is traced from the surface it is emitted to the surface it is finally absorbed, considering any interaction it may have with the rest of the surfaces of the geometry. These interactions include specular and diffuse reflections and transmissions. However, a large number of rays need to be traced to achieve precise results, making this process highly computationally expensive. Because it is assumed that rays do not interact between each other, the calculation of each ray is independent from the rest, and the computation can be easily parallelized. Because of this, Monte Carlo ray tracing algorithms are very suitable for GPUs, especially the new ones with built-in hardware compute units to accelerate the process of tracing rays within the geometry.
In order to better utilize the GPU hardware capabilities, the geometry surfaces are discretized into triangular meshes. While this approach introduces a triangulation error to the result, the error can be reduced by refining the triangular meshes. Using Vulkan, an open-source, multi-platform standard for low-level access to the GPU hardware, we have developed a code focused on the architecture of the latest GPUs to calculate view factors (VFs) and REFs of STEP-TAS geometry models.
The results show that the GPU code we have developed can compute VFs and REFS with a negligible triangulation error much faster than other commercial software that only uses the CPU. As an example, using a single desktop GPU, we have been able to calculate the VFs and REFs of the Vigil’s PMI instrument Filtergraph model between two to three orders of magnitude faster.
Speaker: Daniel Navajas Ortega (Universidad Politécnica de Madrid)
-
45
-
Thermal Control Newton
Newton
Convener: Romain PEYROU-LAUGA (ESA)-
47
Concept design and preliminary experiments of novel electronics enclosure with phase-change capacitor
High-performance computers designed for space applications face significant challenges related to excessive heat generation and high-power density within confined volumes. These issues arise due to the intense computational demands required for Earth observation space missions, future space data centers and systems in spacecrafts for processing data of all kinds. Managing heat dissipation and power density effectively becomes crucial to ensure the reliability of these advanced computing systems in the harsh environment of space. To address the challenges of high heat dissipation and overheating of the unit, KP Labs team proposes phase change material capacitor to reduce the thermal loads of the electronics.
In the study we present the concept stage of the heat capacitors development dedicated for electronics enclosures. The numerical model of the breadboard/prototype have been developed in the FloEFD software. The numerical model includes phase change material modelled with simplified formula. The hermetic chassis was designed and manufactured. Current preliminary vessel was filled with 40 grams of n-eicosane. Tests have been conducted in TVAC. The effect of PCM capacitor was observed during the experiment together with peculiar behavior of the material during the phase change. The numerical model was validated against the experimental results and such a model will be used in further development of the prototype which will consider using internal fins within the vessel to reduce the main drawback of PCM which is its low thermal conductivity. Further investigation is needed to assess the feasibility of technology is real space applications.Speaker: Artur Jurkowski -
48
Smart thermal control with 2D flexible passively self-regulating heater
The thermal control of satellites requires technologies that can effectively heat sensitive areas, while alleviating the constraints associated with this need.
Nowadays each piece of equipment or subsystem may require one or even several heating lines, which imposes constraints such as:
- Need to multiply the lines in order to guarantee a certain temperature homogeneity
- Each line requires thermistors and connectors as well as the bandwidth associated with the signal levels (TM/TC, etc.).
- The choice of line control (ON/OFF, PID, etc.) must be chosen, challenged and validated,
- In the case of the use of a mechanical thermostat, the lifetime constraint must be assessed and justified,
- Depending on the criticalities, the lines can be redundant in order to avoid prohibitive failures.
Therefore, the development of a flexible passively self-regulating heater would greatly reduce the efforts of thermal regulation. This innovative type of heater is based on the PTC (Positive Temperature Coefficient) effect. The small company Heatself has already proven the effectiveness of this phenomenon by developing flexible 1D self-regulating heaters (heating cables). This work deals with the proof of concept of a new 2D flexible self-regulated heaters with a direct application as passive smart thermal control of electronic units inside the satellite. The paper presents the physical and operation principle of the technology, the prototyping phase and the functional and operational testing in simulated space environment.Speakers: Mr Philippe Paul Bert (Heatself), jean-paul Dudon (THALES) -
49
Qualification Level Testing of Graphene Thermal Straps for the use on the WFI Instrument
The camera head of the Wide Field Imager (WFI), which is to fly on the x-ray telescope ATHENA, is a compact system requiring the integration of three separate temperature regions. One will be the environment temperature of the instruments support structure. The other two temperature environments are governed by the requirements of the detector front end electronics and the detector itself. To remove the heat from the system generated by the electronics of the detector, two dedicated thermal interfaces are provided. To mechanically decouple the detector system from the thermal interfaces the use of thermal straps is necessary. Due to the small space available in the camera head to implement thermal straps, the requirement on the thermal conductance for the connection is very high. The decision has been made to use graphene thermal straps that are wrapped in double-aluminized mylar. To assess their suitability for the project, a qualification campaign is carried out. The thermal straps are tested for their thermal performance, structural stability and particle shedding, thermally cycled and outgassed. The thermal straps will be placed close to the detector system. Hence the particle and outgassing contamination are of particular interest. In the current presentation, the qualification tests are presented.
Speaker: Jan Philipp Möller (Max Planck Institute for extraterrestrial Physics)
-
47
-
18:00
Workshop Dinner ESTEC Restautant
ESTEC Restautant
-
-
-
Heat Transport: 2-Phase Einstein
Einstein
Convener: Mr emmanuel caplanne (ESA)-
50
Development and testing of a mechanically pumped loop for active antennae
The satellite telecommunications industry is currently undergoing significant evolutions. Future communication satellites need to accommodate a rapidly growing demand in data transfer, combined with more flexibility. For example, there is a strong need for Very High Throughput Satellites capable of delivering up to Terabyte per second over wide coverage areas. This is only possible when an active phased array antenna is used. However, cooling of active antennas requires the use of a highly efficient thermal control system because it has many heat sources (from hundreds to several thousands), high local heat fluxes (20 W/cm² at evaporator interface), high overall dissipation (around 10 kW), and isothermal requirements on the amplifier chain. These conditions are very difficult to meet with current thermal control solutions (e.g. heat pipes or loop heat pipes), but require a two-phase mechanically pumped fluid loop (MPL). In an MPL, a pump circulates a fluid which evaporates when it absorbs the waste heat from the active antenna. In the IMPACTA project, a demonstrator for such an MPL is being designed and build. This paper describes the test results for the IMPACTA demonstrator. The demonstrator is able to cool a total heat load of 9.8 kW divided over 10 parallel branches with a better than 2°C spatial temperature uniformity over the heat sources. In an active antenna application, the heat load can be unevenly distributed over the different branches. Tests show that even in the extreme case when half of the branches are turned off and the other half are set to full power, no sign of dry-out or too high temperatures is observed, demonstrating the ability of the MPL to cool imbalanced payloads. The demonstrator was tested in 3 different orientations and the test results are similar for all orientations, indicating that the system is not sensitive to gravity effects.
Speaker: Henk Jan van Gerner (NLR) -
51
Comparison of Cu-H2O Heat Pipes and Al- NH3 Heat Pipes for external homogenization of an electronic box
In order to homogenize the temperature distribution over an electronic box, the use of heat pipes is investigated. The operating temperature range is between + 20 °C and + 85 °C. The expected main working range is between + 20 °C and + 55 °C. The total heat dissipation to be transported is 45 W. It is distributed over three locations: Evaporator 1 (top left position): 7 W; Evaporator 2 (top right position): 10 W; Evaporator 3 (Center position): 28 W. The heat is transported to two condenser areas: Condenser 1 (bottom left) and Condenser 2 (bottom right).
Due to the wide specified operating range, a trade-off between Cu-H2O heat pipes and Al-NH3 heat pipes was performed. As it can be looked up in the figure of merit for working fluids, the optimal operating temperature for Cu-H2O HP is above 50 °C and the optimal working range for Al-NH3 HP is up to 70 °C.
The two different heat pipe types differ in the design. The Cu-H2O Heat Pipe is built as an assembly consisting of four L-shaped heat pipes. One HP connecting Evaporator (Evp) 1 and Evp 3, one connecting Evp 2 and Evp 3, one connecting Evp 3 and Condenser (Cond) 1, and one connecting Evp 3 and Cond 2. All four heat pipes are interconnected via the Evp 3 interface by soldering into an aluminium block. The Al-NH3 Heat Pipe are two separate U-shaped heat pipes. The left heat pipe connects Evp 1, Evp 3, and Cond 1. The right heat pipe connects Evp 2, Evp 3 and Cond 2. No direct contact between the left and the right heat pipe exists.
Temperature measurement along the heat pipes were performed at several operating temperatures (20 °C, 50 °C, 75 °C, and 85 °C). In order not to over predict the performance the measurements were performed with a tilt height of 2 mm against gravity. For the operating temperature of 50 °C, tilt measurements (4 mm, 6 mm, and 76 mm (20 ° inclination)) were performed.
As expected, the performance of the Cu-H2O HP increased with higher temperatures above 50°C. The Al-NH3 HPs performed quite well within the defined temperature range, with a decreasing performance above 70°C. However at 85°C the Al-NH3 HPs still transport the specified power. Furthermore, the gradients along the Al-NH3 HPs at high temperatures are still lower than for the Cu-H2O HP Assembly, which is against expectations.
At a vapour temperature of 20 °C high temperature gradients over the Cu-H2O HP are observed (dT = 12 K at the specified heat load). A significant contributor causing the high gradients are the not ideal working point of water. The gradients decrease with higher operating temperatures and reach their optimum working point at around 75°C (dT = 4.4 K at the specified heat load). Due to the split design of the Cu-H2O HP Assembly, the temperature gradient over the Cu-H2O HP assembly is still higher than the gradient over the single Al-NH3 HP’s (dT = 2.1 K) at the specified applied heat load - even at high operating temperatures. As expected, at a tilt height of 76 mm (20° inclination) no operation of the Al-NH3 HP is possible, whereas the Cu-H2O HP Assembly shows only a marginal performance loss.Speaker: Dr Annika Hell (Airbus Defence and Space GmbH) -
52
Chemical Compatibility of Various Working Fluids with Additively Manufactured Materials for Two-Phase Cooling Systems.
Chemical compatibility between the main components of two-phase heat transfer devices is of critical importance for correct operation and stability throughout the device’s operational lifetime. The use of incompatible fluid-metal combinations can lead to corrosion and/or the generation of non-condensable gas (NCG), both of which result in reduction in heat transfer performance or complete device failure.
To verify working fluid and material compatibility, life-testing experiments were conducted across a wide range of fluid-material combinations, with a particular focus on additively manufactured materials using the laser powder bed fusion process (PBF-LB/M). As this is a relatively new technology, the material’s compatibility with different fluids, including ammonia, must be demonstrated before they can be used in future space applications. This work included the design and manufacture of multiple thermosyphon devices, followed by long-term characterisation through gas plug testing. The project aims to provide recommendations of the successful fluid-metal combinations to the community.
Speaker: Dr Colin Butler (University of Limerick) -
53
Experimental characterization of a SiC-Ammonia heat pipe after 2-year storage in room conditions
The increasing demand in image quality provided by forthcoming observation missions needs both to use very low-CTE materials for focal planes, such as Silicon Carbide (SiC), and to accommodate electronics very close to the detector. Such a highly integrated focal plane thus implies an efficient Thermal Control to drain the heat dissipation and ensure a high stability of the detector temperature. One solution could be to design a focal plane with embedded grooved heat pipes, which would drain the heat and make the temperature uniform.
In the frame of a CNES Research & Technology activity, co-funded by CNES, Mersen Boostec manufactured and assembled a SiC-based heat pipe, and CNES performed characterization testing after filling it with ammonia. After this initial test campaign, which demonstrated a healthy behavior, the filled heat pipe has been stored in room conditions during almost two years. Two other test campaigns were carried out to monitor a potential drift in the global performance of the heat pipe.
This presentation focuses on tests results obtained after 9 months of storage and after the storage period.
Speaker: Guillaume Boudier (CNES)
-
50
-
Thermal Analysis Newton
Newton
Convener: Mr Duncan Gibson (Telespazio VEGA UK for ESA)-
54
Trade Off EcosimPro/LMS Amesim for MPL modeling and its co-Simulation with e-Therm
EcosimPro is a versatile mathematical tool that excels in modeling and simulating both continuous and discrete systems, making it particularly adept at non-causal simulation. It is capable of effectively handling Differential-Algebraic Equations (DAE) and Discrete Events, offering applicability across various problem domains. Originally funded by the European Space Agency (ESA) to simulate Environmental Control and Life Support Systems for manned spacecraft like Hermes and Columbus, EcosimPro is now developed and distributed by Empresarios Agrupados A.I.E. Its utility extends beyond the aerospace sector, finding applications in fields such as fluids, chemical processes, control systems, electrical engineering, and propulsion.
Thales Alenia Space (TAS) has developed a Two-phase Mechanically Pumped Loop (2Φ-MPL) for transferring heat from high throughput telecommunication payloads to external rejection radiators. The first deployment of the 2Φ-MPL took place on the SES17 satellite in late 2021. To comprehensively model and simulate the behavior of 2Φ-MPL fluid loops at the system level, a combination of tools was employed. Siemens Amesim was utilized in co-simulation with the TAS e-Therm thermal simulation tool, which incorporates TAS thermal nodal modeling and solving capabilities for satellite design. The e-Therm / Siemens Amesim co-simulation was jointly developed in 2016 by DOREA, the organization responsible for the development and maintenance of e-Therm under the TAS contract. The co-simulation was implemented using the "Generic Co-Simulation Interface" from Siemens imagine.lab library.
In the frame of an ESA contract, the present study aims to assess whether EcosimPro can serve as a suitable alternative to Amesim for conducting simulations of this type. To this end, the first step consists in establishing 2Φ-MPL model with EcosimPro, followed by performing co-simulation of e-Therm with EcosimPro, and finally consolidating EcosimPro's evaluation to draw conclusions.Speaker: François BRUNETTI (Dorea) -
55
SYSTEMA – THERMICA
SYSTEMA – THERMICA
Léa Galeron, Antoine Caugant, Mathieu Lepilliez
(Airbus Defence and Space SAS, Toulouse, France)The presentation will begin with an overview of the two releases of Systema issued the past year, then a segment will be dedicated to the operational validation of the last Long Term Support (LTS) version.
Systema 4.9.2P1 was released last April 2023 to address some issues signalled by users and a new application called Airdrag has been added to the Perturbation packages. This application computes perturbing forces, torques and thermal fluxes resulting from the interaction of the remaining atmosphere particles with the satellite's surfaces.
Systema 4.9.3 has been issued in fall 2023. This new version improves some ergonomic features such as the file selection window or the drag&drop to reorganize shapes at the same level. Moreover the precision of the calculation of orbital parameters (true solar time, true anomaly…) has been improved and it is now possible to change the center of the inertial frames. Some improvements were also performed on the Python API to facilitate the post processing. Thermica also embeds new capabilities such as the export of any real or integer user entities and Thermisol variables in h5 file.
Finally, the adoption of the 4.9.2 version by the Airbus DS thermal community (Toulouse, Friedrichshafen and Stevenage) was performed this year. The methodology and challenges of this transnational software migration as well as the various technical opportunities it generates for users will be detailed.
Speakers: Antoine Caugant, Léa Galeron -
56
Radian: CAD importing and other improvements for thermal analysis software
Radian is a thermal analysis software conceived to provide agility to engineers, both at modelling and computing processes. Our software is accessible through a regular web browser and counts on a scalable network of computing resources in the cloud. Thermal analyses are supported by the Databank, a catalogue of satellite components and other reusable entities. The underlying simulation engine reproduces the orbital environment and the thermal solution.
Over the course of 2023, our team has developed a novel feature that allows importing CAD files into our software and turning them into thermal models. Smart importing consists of a series of routines that analyse the morphology and hierarchy of the CAD file, in order to guide the user through the process of simplifying and optimising the contents of the CAD model.
In addition, several new features have been included both in the user interface and the simulation engine, ranging from new ways of visualising data, to faster and more powerful computing tasks.
Speaker: David Criado -
57
ESATAN Thermal Modelling Suite - Product Developments
ESATAN-TMS provides an advanced thermal modelling environment for the thermal analysis of spacecraft and launch vehicles. The suite is continually being enhanced to meet current and future requirements of space projects, and to support the specific needs of thermal engineers. This presentation will focus on the latest development to be included in the coming ESATAN-TMS 2024.
Speaker: Henri Brouquet
-
54
-
11:00
Coffee Break Einstein and Newton
Einstein and Newton
ESA/ESTEC
Keplerlaan 1 2201 AZ Noordwijk The Netherlands -
Cube Sats Einstein
Einstein
Convener: Malgorzata Solyga-
58
Thermal validation of the Juventas CubeSat in support of the HERA mission to the Didymos Asteroid system.
ESA’s HERA mission launching in October 2024 is the follow-up to NASA’s DART mission, investigating planetary defence measures by impacting the Dimorphos asteroid, part of the Didymos binary asteroid system. HERA’s mission is to measure the momentum transfer from DART as well as catalogue in greater detail the asteroids’ properties. HERA will carry two CubeSats: Milani and Juventas. Juventas with payloads of GRASS: a gravimeter, and JuRa: a Low-Frequency Radar, will assist with the investigation into the makeup of Dimorphos.
This presentation will describe the thermal design and validation of the Juventas Structural Thermal Interface Model (STIM). With a complex thermal environment, the CubeSat is designed for the full mission duration: stowed inside HERA, deployed but still attached to the HERA spacecraft, and when fully commissioned with deployed solar panels and antennas in deep space (1.26AU to 1.72 AU).
Albeit a simplified model, the STIM was designed to have the same structural, thermal, and electrical interfaces representative of the flight model. It was used to validate a Finite Element Analysis (FEA) model which replicated the mass and specific heat capacity of the STIM within 5% and 10% respectively.
The primary validation effort was the Thermal Balance Test (TBT) done at two plateaus: a hot TBT was performed at 10DegC to investigate the dissipations of the spacecraft and a cold TBT was performed at -10DegC to investigate the heaters and insulating spacers on the propulsion tank. A COMSOL FEA model and Lumped Parameter Model (LPM) were created of the STIM in a TVAC chamber, replicating the environmental conditions of the TBT. Comparing the results of the TBT test to the FEA model and LPM; allowed for the validation of the FEA modelling technique. The revised assumptions have been updated in the flight model FEA. The difference between the TBT and LPM resulted in a less than 5DegC difference on the spacecraft body. Comparing the results of the thermocouples on STIM, with the equivalent probed nodes on the FEA model, resulted in an average difference of 0.87 DegC during cold validation, and 3.98 DegC for hot validation.
The Juventas flight model is ongoing and is being led by GomSpace Luxembourg and supported by GomSpace Denmark.Speaker: Zoe Townsend (Gomspace) -
59
3Cat-4 Thermal Analysis and Thermal Vacuum Test Campaign
The 3Cat-4 is the fourth member of the CubeSat series of UPC’s NanoSat Lab, selected in ESA Academy’s Flight Your Satellite program in 2017. This mission mission aims at demonstrating the capabilities of nanosatellites, and in particular those based in the 1-Unit CubeSat standard, for challenging Earth Observation (EO) using Global Navigation Satellite System - Reflectometry (GNSS-R) and L - band microwave radiometry, as well as for Automatic Identification Services (AIS). The following study presents the results of the thermal analysis carried out for this mission, evaluating different scenarios, including the most critical cases at both high and low temperatures. The results consider different albedos and orbital parameters with the objective of establishing optimal temperatures to achieve better mission performance within the nominal temperatures and in all operational modes of the satellite.
Additionally, simulation results are included that consider the thermal performance of other materials, such as Kapton, as well as the redesign of the optical properties of the satellite’s solar panels.Speaker: Jeimmy Nataly Buitrago Leiva (Polytechnic University of Catalonia) -
60
Thermal contact conductance in smallsats
It is generally known that thermal contact resistance between two bodies is a function of pressure, hardness, and thermal conductivity [1]. In most engineering cases there is a constant trade-off between the demands of the thermal design and other requirements. It is especially true for typical cubesat applications [2]. This means it may not always be feasible to apply high pressure or utilize highly thermally conductive materials characterized by sufficient hardness.
In order to address these problems at early stages of the design phase, simulation tools are used in which contact thermal resistance is a parameter defined by a thermal engineer. Since it is not always possible to perform experiments on thermal interfaces considered in the analysis, a modelling approach based on [3], [4] or [5] work is preferred. Some of them considered simplification of vacuum conditions [6] which is actually beneficial for approach used in this work. Those models usually discuss flat plates of sufficiently thick layers of material with uniform pressure distribution that is kept constant in time. These might not be always the case: pressure can be considered uniform only in direct neighborhood of a point where the force is applied (for example bolted nut connection); surfaces might not be flat (on micro scale they always have some roughness, but they also might not be planar at all, with curved contact area); force (and pressure) can change in time (deteriorating contact conductance and increasing thermal induced stresses).
Those variables were considered in this work analytically and numerically for a few types of connections, mainly bolted joints. Moreover, connections of more advanced shapes (threaded inserts) with variable pressure distribution were analyzed. Comparisons between interfaces utilizing thermal interface materials and bare metal connections were performed.Conclusions derived from this investigation were used in a practical approach to analytically determine the equivalent thermal conductivities of bolted joints of the Intuition-1 satellite. The aim was to replace complex geometric elements in the numerical model of the satellite with one-dimensional conductors of specified overall thermal resistance. Additionally, experimental work was performed to establish contact resistance of reference copper and aluminum plates with different degrees of roughness. This allowed to choose appropriate contact conductance model. Due to small interface areas and relatively high contact pressures typical to nanosatellites, the analytical models for contact conductance were applicable. By utilizing the described method in the numerical analysis of the satellite, convergence between simulation results and measurements in the thermal-vacuum chamber was achieved.
References
[1] M.M. Yovanovich. “Four decades of research on thermal contact, gap,
and joint resistance in microelectronics”. In: IEEE Transactions on
Components and Packaging Technologies 28.2 (2005), pp. 182–206. doi:
10.1109/TCAPT.2005.848483.
[2] P. B. Hager et al. “Contact Conductance in Common CubeSat Stacks”.
In: (2019), p. 14.
[3] M. Yovanovich. “Micro and Macro Hardness Measurements, Correla-
tions, and Contact Models”. In: Collection of Technical Papers - 44th
AIAA Aerospace Sciences Meeting 16 (Jan. 2006). doi: 10.2514/6.
2006-979.
[4] M. G. Cooper, B. B. Mikic, and M. M. Yovanovich. “Thermal Contact
Conductance”. In: International Journal of Heat and Mass Transfer 12
(1969), pp. 279–300.
[5] A. Majumdar and C. L. Tien. “Fractal Characterization and Simulation
of Rough Surfaces”. In: Wear 136.2 (1990), pp. 313–327. doi: 10.1016/
0043-1648(90)90154-3.
[6] M. M. Yovanovich and H. Fenech. “Thermal Contact Conductance of
Nominally Flat Rough Surfaces in a Vacuum Environment”. In: Ther-
mophysics and Temperature Control of Spacecraft and Entry Vehicles.
Ed. by G. B. Heller. Vol. 18. New York: Academic, 1966, pp. 773–794.Speakers: Kacper Kuta, Radosław Paluch
-
58
-
Thermal Testing Newton
Newton
Convener: Mr Gunnar Sieber (European Space Agency)-
61
On-Ground Calibration Target for the MetOp-SG Ice Cloud Imager – the TCS from first idea to operation
The On-Ground Calibration Target (OGCT) for the Ice Cloud Imager (ICI), to be flown on the Metop-SG Satellite B, has been developed, built and sub-system tested in a joint effort by IABG mbH (thermal design, modelling & testing, thermal control sub-system manufacturing), Thomas Keating Ltd. (radio frequency & mechanical design, mechanical manufacturing), and the Institute of Applied Physics of University of Bern, IAP (radio frequency modelling & testing) under Airbus Defence and Space España (ASE) project management.
The OGCT consists of two microwave blackbodies in a wedge design, with fine temperature control achieved by liquid nitrogen cooling and electrical heaters. The challenging key requirements for thermal control include accurate knowledge of absolute temperature (better than ±0.1 K), highly stable control of target temperature (better than 0.1K / 5 min) and a uniform temperature distribution across the blackbody area (lower than 0.3 K) – all to be achieved over the full temperature range from 80 K to 335 K.
According to IABG’s heritage as a test centre, the development approach heavily relied on testing in all stages of development, combined with thermal modelling and analysis. After a successful thermal vacuum qualification test in early 2020, final acceptance of the OGCT was achieved. Since then, the OGCT has successfully performed radiometric calibration of the Ice Cloud Imager’s EM in December 2020, PFM in 2022 and FM2 in 2023. First operation of the OGCT on spacecraft level is planned for the Thermal-Vacuum test of MetOp-SG Satellite B.
The presentation gives an overview over the thermal control system of the OGCT: the evolvement of the design is presented, starting with early design concepts from 2015, with a focus on the main challenges and lessons learnt along the way, as well as the results of the thermal vacuum acceptance tests.
Speaker: Mr Daniel Winter (IABG mbH) -
62
Performance of Cryogenic thermal test setup for ARIEL FGS instrument
The Atmospheric Remote-sensing and Infrared Exoplanet Large-survey (ARIEL) is a space observatory and the fourth medium-class (4M) mission of the European Space Agency's (ESA) Cosmic Vision programme. One of the instruments on board ARIEL is Fine Guidance System (FGS). This optic sensor provides high-precision pointing information for the telescope which is an input to its attitude control system. Spacive Sp. z o.o. is responsible for the design of the thermal test setup in the thermal vacuum chamber for the the Space Research Centre of the Polish Academy of Sciences (CBK PAN), which is responsible for the development of the FGS instrument.
In this paper we are presenting design of the test setup in the Thermal Vacuum Chamber, which requires maintaining different interfaces with stable temperature of 30K and 90K for the FGS instrument and supporting electronics. Moreover, we presents the results of thermal analyses, validation test campaign of completed setup and model correlationSpeaker: Piotr Osica (Spacive Sp. z o.o.) -
63
WFI Large Detector Quadrant Thermal Test
The Wide-Field-Imager (WFI) instrument is one of two instruments planned to fly on the ATHENA observatory. At its current capabilities, WFI can image incoming X-ray photons in the energy band from 0.2 eV up to 15 keV and a time resolution of less than 5ms with its Large Detector (LD) Array . It also has the provision for high-count rate measurements in the same energy band using a Fast Detector (FD), with a photon-counting time resolution of 80µs. Mechanically, the Large Detector Array of the WFI is composed of 4 identical Large Detectors quadrants. Each Large Detector quadrant consists of a 512 x 512 pixel DEPFET (depleted p-channel field effect transistor) sensor with dedicated read-out Front End Electronics (FEE). The FEE ASICs (Application-Specific Integrated Circuit) and the DEPFET sensor are linked through bond-wires. Both the DEPFET sensor and the FEE are supported using separate frames that are thermally decoupled to reduce the parasitic heat between them since DEPFET sensor operates at a much lower temperature compared to the FEE. The DEPFET sensor and the FEE PCB are both bonded to their frames using adhesives.
Two critical thermo-mechanical aspects of the design are identified: the stresses induced in adhesive bonds during cool-down to operating temperatures and stresses in the bond-wires due relative displacement between the DEPFET sensor and the FEE ASICs caused by their thermo-elastic deformation.
A single LD-quadrant is tested in a ‘'qualification-like’' manner by cycling it through the operational and non-operational temperatures to verify the above-mentioned aspects of design. The test is carried out at the in-house LUCHS test facility of the Max Planck Institute for Extraterrestrial Physics with a setup consisting of a small vacuum chamber, a Stirling cooler, heater power supply and control, and temperature measurement equipment. The presentation describes the test rationale, test environment and the success criteria. Further, the results of the test are presented and discussed.
Speaker: Anirudh Mukund Saraf (Max Planck Institute for Extraterrestrial Physics)
-
61
-
Opening: Closure Newton
Newton
-
64
Closure
Closure of the workshop
Speaker: Dr Harrie Rooijackers (ATG-Europe)
-
64
-
13:15
Lunch Break ESTEC Restaurant
ESTEC Restaurant
-